July 21, 2025
LIMS Quality Indicators: Ensure Precision in Your Lab
Table of Content
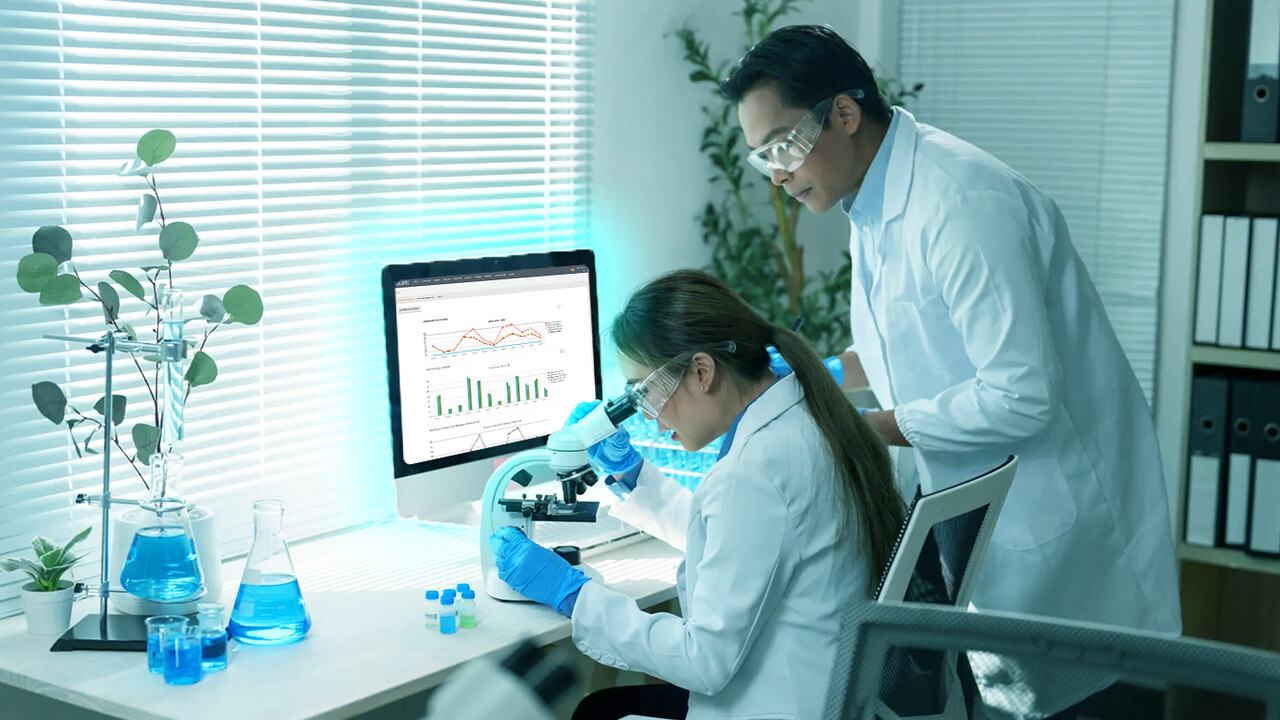
In today’s high-stakes environment, there’s no room for guesswork—laboratories need precision, speed, and control. That’s where quality indicators and visual dashboards come in. These powerful tools are game-changers for industries where accuracy is non-negotiable—whether it’s environmental testing, food safety, or industrial analysis. Integrated into a cutting-edge Laboratory Information Management System (LIMS), they deliver real-time insights, streamline operations, and drive smarter, faster decisions.
LIMS software doesn’t just automate workflows—it transforms them. By centralizing critical data, it gives you a 360° view of your lab’s performance, empowering you to lead with confidence and stay ahead of the curve.
Why are quality indicators and dashboards crucial in laboratories?
Modern laboratories are not only looking to deliver accurate results, but also to maintain operational excellence and meet stringent regulatory requirements. Quality indicators and dashboards for laboratories are vital management resources that:
- Create visual and intuitive dashboards.
- Visualize diverse information instantly or historically.
- Facilitate daily monitoring of operations.
- Identify critical trends, patterns, and deviations.
- Support strategic decisions critical to the business.
In this sense, by generating objective measurements and clear references, laboratories can improve the quality of the final product, optimize the efficiency of laboratory processes, reduce operating costs, and ultimately gain a significant competitive advantage.
For example, a dashboard can show in real-time the number of pending samples, mean analysis times (TAT) by test type, and error rates, allowing managers to quickly identify problem areas and take corrective action.
Maximizing Lab Efficiency with Key Quality Indicators
The implementation of a robust LIMS system allows the generation and monitoring of essential quality indicators for superior lab data management:
Advanced Laboratory Performance Monitoring
Advanced LIMS systems enable proactive monitoring of laboratory performance through key performance indicators (KPIs). This includes:
- Number of samples processed: To assess capacity and workload. A sudden increase in the number of samples may indicate the need to hire more staff or invest in additional equipment.
- Turnaround Time (TAT): Crucial for customer satisfaction and efficiency. A high TAT can be caused by workflow bottlenecks, understaffing, or equipment issues.
- Rework and Re-analysis Rate: A direct indicator of the quality and efficiency of the initial processes. A high rework rate may indicate problems with testing methods, staff training, or reagent quality.
- Compliance with regulatory requirements: To ensure compliance with standards such as NELAP/TNI, ISO 17025 and/or EPA standards, FDA regulations or other specific sectoral regulations. Failure to comply with regulations can result in fines, loss of accreditation, or even closure of the laboratory.
This information is critical for identifying bottlenecks, optimizing lab workflows, and ensuring compliance with deadlines and strategic goals.
For example, if the TAT for a specific type of analysis is consistently high, the laboratory can investigate the underlying causes and take steps to optimize the process, such as automating tasks, optimizing analysis protocols, or improving staff training.
Quality Control of the Results
Ensuring the precision and accuracy of analytical results is the cornerstone of a laboratory's credibility. Specific indicators help to:
- Assess the sample error rate and its impact. A high percentage of sample errors may indicate problems with sample collection, transportation, or storage.
- Measure the variability of results (accuracy). High variability may indicate problems with equipment, methods of analysis, or staff training.
- Compare results with reference values and control materials. This helps to detect systematic or random errors.
- Detect systematic or random errors early.
- Implement corrective and preventive actions effectively. For example, if a systematic error is detected in a piece of equipment, calibration or preventative maintenance can be performed to correct the problem.
Evaluating and Improving Customer Satisfaction
The quality of the services provided by the laboratory directly impacts the perception and loyalty of the client. The quality indicators provide a clear view of:
- Response time to requests: From the receipt of the sample to the delivery of the report. A slow response time can result in customer churn.
- Efficiency in solving problems or queries: The ability to quickly resolve customer issues is crucial to maintaining customer satisfaction.
- Compliance with customer-specific requirements (SLAs – Service Level Agreements): Failure to comply with SLAs may result in penalties or loss of contracts.
These indicators provide an objective perspective on perceived quality and allow the laboratory to take proactive steps to improve the customer experience. For example, if customers complain about turnaround time, the lab can implement a sample tracking system to identify bottlenecks and optimize workflow.
Practical Applications of Indicators in LIMS-powered Laboratory Processes
When it comes to optimizing laboratory processes, the use of indicators through a LIMS allows:
Greater Control of Resources:
- Scheduling and monitoring equipment maintenance. A LIMS can generate automatic alerts when equipment needs maintenance, preventing breakdowns and downtime.
- Control of inventory and stock of laboratory supplies, avoiding breakages or excesses. A LIMS system can track reagent consumption and generate automatic orders when levels are low.
Accurate Measurement of Rework and Re-analysis Rates:
- Identifying areas for improvement in procedures. A LIMS can track the causes of rework and reanalysis, allowing the lab to identify problem areas and take corrective action.
Optimization of the Time to Release Results:
- Detecting potential bottlenecks in the analysis flow. A LIMS can identify process steps that are causing delays and allow the lab to optimize workflow.
Comprehensive Monitoring of Laboratory Efficiency:
- From sample receipt to invoicing. A LIMS can provide a comprehensive view of laboratory performance, allowing managers to identify areas for improvement and make informed decisions.
The Strategic Role of LIMS Software in the Generation of Quality Indicators
A LIMS system not only collects data but transforms it into valuable information. It allows the creation of custom dashboards that display key performance indicators (KPIs) in real-time. These dashboards can be configured to display specific information for different roles within the lab, from lab technicians to managers. For example, a lab technician can use a dashboard to monitor the status of samples under their responsibility, while a manager can use a dashboard to monitor the overall performance of the lab.
In addition, a LIMS can generate automatic reports that are sent to managers on a regular basis. These reports can include information on the number of samples processed, average analysis times, error rates, and other relevant KPIs. This information allows managers to make informed decisions about resource allocation, process optimization, and quality improvement.
Conclusion
Quality indicators generated by a LIMS are not just metrics; they are the cornerstone of modern, efficient and continuous improvement-oriented laboratory data management. They provide valuable, actionable insights to monitor performance, control the quality of analytical results, and evaluate customer satisfaction holistically.
By strategically using these indicators, laboratories can optimize their internal processes, ensure compliance with demanding regulatory requirements, and offer the highest quality services. This not only contributes to the credibility and reliability of your analyses but also strengthens your position in the market.
Therefore, investing in a robust and efficient LIMS system, capable of generating and visualizing quality indicators for relevant laboratories, is a critical decision to achieve success and sustained operational excellence. A modern LIMS should be easy to use, configurable, and able to integrate with other laboratory information systems, such as analysis equipment and quality management systems.
Transform your lab today with myLIMS: Visualize Success with Advanced Quality Indicators
If you are looking to optimize management, ensure quality and boost the efficiency of your laboratory, myLIMS is the solution. Discover how our dashboards can be the engine of digital transformation in your company, providing a clear and real-time view of your operations. Let myLIMS be the change you need and start the digital transformation in your company today.
Get started!
Best-in-class LIMS, built for your success
See what makes Confience different. Speak with a member of our team.
Schedule a Demo